AQL CHART
Acceptable Quality Limit
Acceptable Quality Limit (AQL) for Product Inspections:
In today’s quality-conscious market, the Acceptable Quality Limit (AQL) serves as a vital tool in ensuring product excellence. By setting appropriate AQL levels, organizations can maintain high-quality standards, reduce the risk of delivering defective products, and protect their brand reputation. AQL, when complemented by robust sampling plans and inspection techniques, provides a systematic approach to quality control. However, organizations should view AQL as part of a broader quality management system and continuously strive for process improvement to drive sustainable quality outcomes and customer satisfaction.
For example, an AQL of 1.5 – 2.5 – 4.0 means that for a particular inspection, the acceptable quality level for critical defects is 1.5%, for major defects is 2.5%, and for minor defects is 4.0%.
The specific AQL values are determined based on factors such as the product’s intended use, industry standards, customer expectations, and risk assessment. Different industries and products may have varying AQL requirements. It’s important for organizations to establish appropriate AQL levels based on their specific needs and quality goals.
In performing products sampling inspection, IQMS exclusively applies the ISO 2859 (ANSI/ASQC Z1.4-2003), sampling standard which specifies a sampling scheme: Acceptable Quality Level (AQL), to find whether the lot order has met the client’s specifications. Clients may request us to use an alternative standard if they have special requirements.
How to use the AQL Table?
There are basically two tables. The first one tells you which ‘code letter’ to use. Then, the code letter will give you the sample size and the maximum number of defects that can be accepted.
Table 01: Sample Size Code Letters

How to read this table?
Follow the example: Assume your ‘lot size’ is comprised between 1,201 pcs and 3200 pcs, and that your inspection level is ‘II’. Consequently, the code letter is “K”.
Table 02: Single Sampling Plans for Normal Inspections
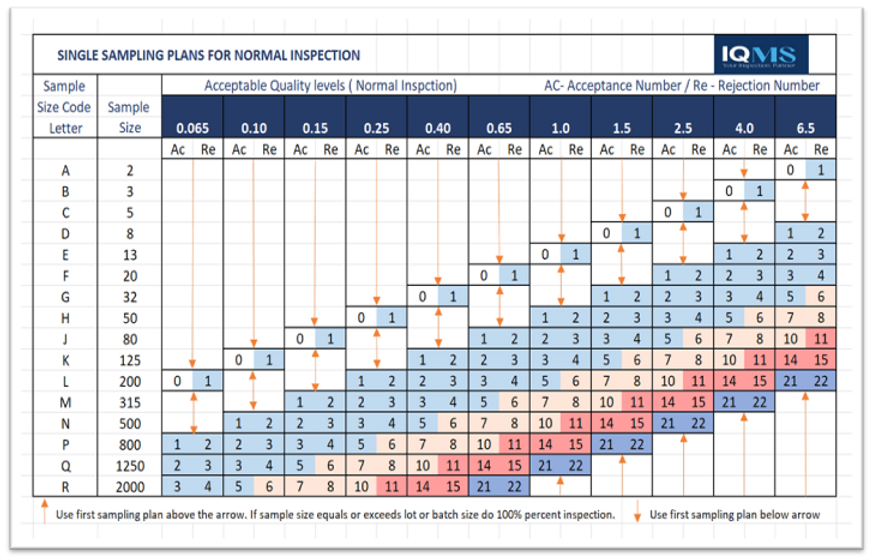
How to read this table?
Our code letter is “K”, so you will have to draw 125 pcs randomly from the total lot size. Besides, I assume you have set your AQL at 2.5% for major defects and 4.0% for minor defects. Therefore, here are the limits: the products are accepted if NO MORE than 7 products with major defects AND NO MORE than 10 products with minor defects are found. For example, if you find 11 products with major defects and 11 products with minor defects, the products are refused. If you find 4 with major defects and 6 with minor defects, they are accepted.
1. Understanding Acceptable Quality Level (AQL):
The Acceptable Quality Limit (AQL) is a statistical tool used in quality control to determine the maximum number of defective units that can be considered acceptable in a given batch of products. It establishes a threshold beyond which the batch is deemed unsatisfactory and requires corrective action. AQL is commonly expressed as a numerical value, often represented as a percentage or a ratio.
2. Importance of AQL in Product Inspections:
AQL plays a pivotal role in product inspections as it provides a quantitative basis for evaluating product quality. By setting a predetermined AQL level, organizations can define the allowable number of defects in a batch, ensuring that only products meeting the specified quality criteria are released to the market. This helps in minimizing the risk of delivering substandard goods to customers, maintaining brand reputation, and reducing potential liabilities.
3. Setting AQL Levels for Different Product Types:
AQL levels can vary depending on the nature of the product being inspected. For instance, industries such as medical devices or aerospace may require extremely low AQL levels due to the critical nature of their products. On the other hand, consumer goods like clothing or toys may have relatively higher AQL levels. It is crucial for organizations to assess the inherent risks associated with their products and establish appropriate AQL levels accordingly.
4. Essential AQL Table Parameters: What You Need to Know
1. Lot Size:
The lot size refers to the quantity of items in a given batch according to ISO 2859. For multiple products ordered, each product is treated as a separate lot, with its quantity representing the lot size. In the case of a single product order, the total batch quantity becomes the lot size.
2. Inspection Level:
The inspection level determines the extent of inspection required. Table 1 provides three general inspection levels: I, II, and III. Unless specified otherwise, it is recommended to use level II. Level I can be chosen when less discrimination is needed, while level III is preferable for situations demanding greater discrimination. Additionally, Table 1 includes four special levels (S-1, S-2, S-3, and S-4) for cases where smaller sample sizes are necessary, and higher sampling risks can be accepted.
3. AQL Limits:
The AQL (Acceptable Quality Level) limits define the maximum acceptable process average for a continuous series of lots during acceptance sampling. It is essential to determine AQL limits that are appropriate for your market. If your customers have strict quality standards and accept very few defects, it may be necessary to set lower AQL values for both major and minor defects.
4. AQL Defects:
In production quality control, defects are typically categorized into three types: Critical, Major, and Minor. Understanding and classifying defects according to their severity is crucial for effective quality assessment and control.
Interpretation of defects may vary among different inspection companies. However, importers and suppliers can find common ground by establishing an Acceptable Quality Limit (AQL) standard that suits both parties, taking into account the level of risk they are willing to assume. Once the AQL standard is mutually agreed upon, it becomes a reference point during pre-shipment inspections.
To determine the acceptable percentage of each defect type in a shipment, order, or batch, you can utilize resources such as the AQL chart, AQL table, AQL sampling plan table, AQL sampling chart, or the AQL calculator. These tools aid in setting appropriate quality levels and ensure that the agreed-upon AQL standard is met during inspections.
Critical Defects:
Critical defects represent the most severe category of defects according to the Acceptable Quality Limit (AQL) table. Importers typically adopt a zero-tolerance policy for critical defects (AQL of 0.0). This means that if even a single critical defect is found during the inspection of the chosen sample size, the entire order will be considered a failure.
The criteria used to identify critical defects include:
Possessing a safety hazard to the intended user
Being the cause of product recalls
Resulting in brand-damaging defects
Examples of critical defects may include:
Presence of mold
Garment with a broken needle
Items with rust
Products having exposed nails or sharp edges
Packaging with hazardous sharp points or edges
Missing local language of the destination
Loose assembly, damage, or lack of insulation tube covering for power switches and connectors
Major Defects:
Less severe than critical defects, major defects are generally allowed in restricted quantities. Importers commonly set the AQL standard limit at 2.5 for major defects.
The criteria used to classify a defect as “Major” are as follows:
It impacts the performance or functionality of the product.
It affects the product’s specifications.
It leads to the end customer’s refusal to purchase or return the product.
Examples of major defects include:
Fabric with holes or tears.
Industrial components with dimensions out of tolerance.
Skipped stitches
Furniture items with uneven legs.
Footwear items with excessive glue.
Minor Defects:
Many importers adopt an AQL standard of 4.0 for minor defects, which represents the least severe category. However, even minor defects can lead to order rejection if found in substantial numbers.
The criteria to identify a minor defect are as follows:
It does not affect the functionality or use of the product.
It is barely noticeable at arm’s length.
It is unlikely to cause a return or render the product unsellable.
Examples of minor defects include:
Untrimmed threads on a garment or plush toy.
Minor color shading.
Removable small dust particles.
Hidden dent marks.