Apparel quality management refers to the processes, systems, and practices put in place by companies and organizations involved in the apparel and textile industry to ensure that their products meet established quality standards and customer expectations. Quality management in the apparel industry is crucial for producing garments that are safe, durable, and in compliance with regulatory requirements.
Here are some key aspects and components of apparel quality management:
- Quality Control (QC): This involves inspecting and testing garments at various stages of the production process to identify and rectify any defects or deviations from quality standards. QC can include visual inspections, measurements, and testing for factors like colorfastness, strength, and fabric quality.
- Quality Assurance (QA): Quality assurance encompasses the processes and procedures designed to prevent defects and ensure consistent quality. It involves setting quality standards, implementing quality management systems, and conducting audits to ensure compliance with these standards.
- Supplier and Vendor Management: Apparel companies often work with multiple suppliers and manufacturers. Effective quality management includes selecting reliable suppliers, setting quality expectations, and establishing clear communication channels to address quality issues promptly.
- Testing and Standards Compliance: Apparel quality management includes testing products to ensure they meet industry and regulatory standards. This can involve safety testing, flammability testing, and compliance with international standards such as ISO and ASTM.
- Traceability: Traceability involves tracking the production process from raw materials to finished products. It helps identify the source of quality issues and facilitates recalls if necessary.
- Employee Training: Properly trained employees are essential for maintaining consistent product quality. Training programs can cover quality control techniques, compliance with standards, and best practices.
- Continuous Improvement: Apparel companies strive for continuous improvement in quality management processes. This involves analyzing data, identifying areas for improvement, and implementing changes to enhance product quality and efficiency.
- Customer Feedback and Complaint Handling: Companies should have mechanisms in place to gather customer feedback, address complaints, and use this information to improve product quality and customer satisfaction.
- Sustainability and Compliance: In today’s apparel industry, sustainability and ethical considerations are increasingly important. Quality management may also encompass compliance with environmental and social responsibility standards.
- Risk Management: Identifying and mitigating risks related to product quality, such as supply chain disruptions or production delays, is another aspect of quality management.
Effective apparel quality management helps companies produce garments that meet or exceed
customer expectations, reduce product recalls and returns, and maintain a positive brand reputation
in the competitive fashion market.
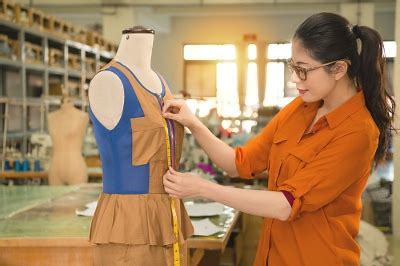
Title: Quality Control vs. Quality Assurance: A Comprehensive Comparison
In the realm of manufacturing and product development, the pursuit of excellence hinges on an unwavering commitment to quality. Quality Control (QC) and Quality Assurance (QA) are two indispensable components that play distinct roles in ensuring product quality. Understanding the differences between these two processes is crucial for delivering superior products.
Quality Control (QC): Defending the Finished Product
Quality Control is a product-centric process primarily concerned with the inspection, testing, and measurement of the final product or its components. It seeks to identify and rectify defects or deviations from established quality standards. Key characteristics of QC include:
- Product Focus: QC revolves around the end product. It involves meticulous inspection and testing to ensure that the final output aligns with predetermined quality criteria.
- Reactive Nature: QC is inherently reactive. It intervenes after the product has been produced and aims to identify and rectify issues or defects that may have occurred during the production process.
- Activities: QC activities include visual inspections, product testing, statistical process control (SPC), and the detection and correction of defects. It acts as the last line of defense before products reach the customer.
- End-of-Process Timing: QC typically takes place at the final stages of production, just before or after the product is completed. It ensures that the product meets established quality standards.
Quality Assurance (QA): Proactively Ensuring Quality
Quality Assurance is a process-oriented approach to quality management, focused on preventing defects from occurring in the first place. It emphasizes the establishment of systems, standards, and procedures that create consistent, high-quality products. Key characteristics of QA include:
- Process-Centric: QA is not product-centered; it’s process-centered. It concentrates on creating and maintaining systems that consistently produce high-quality products.
- Proactive Approach: QA is forward-looking and prevention-oriented. It ensures that processes are meticulously followed, and it addresses the root causes of potential defects to prevent them from occurring.
- Activities: QA activities encompass setting quality standards, implementing Quality Management Systems (QMS), conducting audits, and ensuring that processes are followed correctly. It instills a culture of quality within the organization.
- Throughout the Production Process: QA activities are continuous and integrated into every stage of the production process. From product design and development to manufacturing and beyond, QA is a persistent presence.
In Conclusion: A Harmonious Synergy for Excellence
In the quest for superior product quality, QC and QA are not opposing forces but rather complementary components of an integrated system. QC provides the essential final check to ensure that the product meets specified quality criteria, while QA creates a culture of quality and actively prevents defects from arising. Together, they work harmoniously to uphold standards, reduce defects, and ensure a consistent, high level of product quality.
The effective interplay of QC and QA is vital for delivering products that not only meet industry standards but exceed customer expectations. In the world of quality management, they are inseparable allies in the pursuit of excellence.
Quality is more than a goal; it’s a commitment to delivering the best to the customer. It’s about maintaining a high standard of product quality as a guiding principle in the manufacturing process.
what is the best way to educate our employees for importance of quality of product?
Educating employees about the importance of product quality is essential for maintaining high standards and ensuring customer satisfaction. Here’s a comprehensive approach to educate your employees effectively on this topic:
- Training and Workshops:
- Conduct regular training sessions and workshops on quality control and assurance processes.
- Provide hands-on training, where employees can practice quality-related tasks.
- Include case studies and real-life examples to illustrate the impact of product quality on customer satisfaction.
- Quality Policy and Objectives:
- Develop a clear and concise quality policy that outlines the organization’s commitment to quality.
- Set specific quality objectives that align with the company’s goals, and communicate them to all employees.
- Ensure the quality policy and objectives are visible throughout the workplace.
- Clear Expectations:
- Define quality standards and specifications for products clearly.
- Provide employees with detailed guidelines and checklists for quality control and assurance processes.
- Communicate expectations for individual and team contributions to quality.
- Regular Feedback and Recognition:
- Establish a feedback mechanism that allows employees to report quality issues and suggest improvements.
- Recognize and reward employees for their contributions to maintaining and improving product quality.
- Use performance evaluations as an opportunity to discuss and reinforce the importance of quality.
- Engagement and Involvement:
- Encourage employees to take ownership of product quality by involving them in quality improvement initiatives.
- Create cross-functional quality teams to address specific quality challenges.
- Seek input and ideas from employees for enhancing quality processes.
- Quality Culture:
- Foster a culture of quality throughout the organization, starting from the leadership team.
- Lead by example and demonstrate a commitment to quality at all levels.
- Encourage open communication and a willingness to learn from mistakes.
- Customer Feedback:
- Share customer feedback, reviews, and complaints with employees to illustrate the direct impact of quality on customer satisfaction.
- Encourage employees to take customer feedback seriously and use it as a tool for improvement.
- Continuous Improvement:
- Emphasize the concept of continuous improvement and the role of each employee in making incremental quality enhancements.
- Implement quality circles or brainstorming sessions to generate ideas for improvement.
- Quality Metrics and Key Performance Indicators (KPIs):
- Establish quality metrics and KPIs that can be tracked and shared with employees.
- Regularly review and discuss these metrics with employees to track progress and identify areas for improvement.
- Documentation and Resources:
- Provide employees with access to relevant quality documentation and resources.
- Ensure employees have the necessary tools and equipment to perform quality-related tasks effectively.
- Regular Communication:
- Maintain open and transparent communication channels for discussing quality-related issues and progress.
- Use team meetings, email updates, and other forms of communication to reinforce the importance of quality.
- Quality Champions:
- Appoint or recognize individuals within the organization as “quality champions” who can lead by example and inspire others in matters of quality.
Remember that educating employees about the importance of product quality is an ongoing process. It requires consistent reinforcement and a commitment to a culture of quality throughout the organization. Additionally, involving employees in quality improvement initiatives can help them feel a sense of ownership and responsibility for the products they produce.